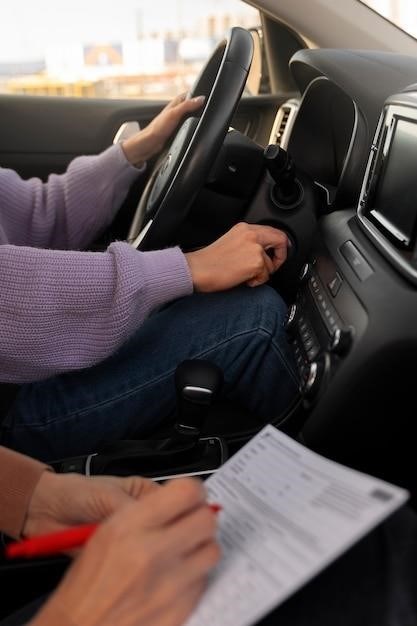
ab 525 drive manual
PowerFlex 525 Drive Manual⁚ A Comprehensive Guide
This manual provides a comprehensive guide to the PowerFlex 525 drive‚ covering everything from its overview and technical specifications to installation‚ configuration‚ communication protocols‚ troubleshooting‚ and safety precautions. It also explores various applications and use cases‚ making it an invaluable resource for anyone working with this drive.
Introduction
The Allen-Bradley PowerFlex 525 drive is a versatile and robust adjustable frequency AC drive designed for a wide range of industrial applications. This manual serves as a comprehensive guide to understanding‚ installing‚ configuring‚ and operating the PowerFlex 525 drive‚ empowering users to maximize its capabilities and ensure optimal performance. This manual provides detailed instructions‚ diagrams‚ and technical specifications to assist users in navigating the intricacies of the PowerFlex 525 drive‚ from basic setup to advanced programming.
Whether you are a seasoned engineer or a novice user‚ this manual aims to equip you with the necessary knowledge and skills to effectively utilize the PowerFlex 525 drive. The manual covers various aspects of the drive‚ including installation‚ wiring‚ configuration‚ communication protocols‚ troubleshooting‚ and safety precautions. It also explores different applications and use cases‚ offering insights into the diverse ways this drive can be implemented in industrial settings.
This manual is organized into various sections‚ each focusing on a specific aspect of the PowerFlex 525 drive. By following the step-by-step instructions and referring to the provided diagrams‚ users can confidently install‚ configure‚ and operate the drive. The manual also emphasizes safety precautions‚ ensuring that users can operate the drive safely and responsibly. This comprehensive guide will serve as a valuable resource for users throughout their journey with the PowerFlex 525 drive.
PowerFlex 525 Drive Overview
The Allen-Bradley PowerFlex 525 drive is a compact and powerful adjustable frequency AC drive designed for industrial applications requiring precise motor control and flexible mounting options. This drive offers a power rating of 0.4…22 kW (0.5…30 Hp) with global voltage classes of 100…600V‚ making it suitable for a wide range of motor sizes and operating environments. The PowerFlex 525 drive incorporates advanced features and functionalities‚ enabling users to tailor its performance to specific application needs.
The drive features a user-friendly interface that simplifies configuration and operation. It boasts a robust design‚ ensuring reliable performance in demanding industrial settings. The PowerFlex 525 drive supports various communication protocols‚ including EtherNet/IP‚ DeviceNet‚ and RS-485‚ allowing seamless integration with other industrial automation systems. This drive also offers advanced control features‚ such as PID control‚ torque control‚ and position control‚ providing users with greater flexibility and precision in motor control.
The PowerFlex 525 drive is designed to meet industry standards for safety and reliability. It incorporates various safety features‚ including Safe-Torque-Off (STO) and Safe Stop 1 (SS1)‚ ensuring a secure operating environment. The drive is also compliant with international EMC directives‚ minimizing electromagnetic interference and ensuring compatibility with other equipment in the industrial environment. With its comprehensive features and robust design‚ the PowerFlex 525 drive is a reliable and efficient solution for various industrial applications.
Technical Specifications
The Allen-Bradley PowerFlex 525 drive boasts a range of technical specifications that cater to diverse industrial applications. Its power rating spans from 0.4 kW to 22 kW (0.5 Hp to 30 Hp)‚ accommodating various motor sizes. The drive operates with global voltage classes ranging from 100V to 600V‚ ensuring compatibility with various power supplies. The PowerFlex 525 drive is equipped with an embedded EtherNet/IP adapter‚ facilitating seamless integration with Rockwell Automation’s ControlLogix controllers and other automation systems.
The drive features a built-in encoder interface‚ supporting incremental AB encoder (25-ENC-1) for precise motor position feedback. It incorporates a variety of safety features‚ including Safe-Torque-Off (STO) and Safe Stop 1 (SS1)‚ to ensure a secure operating environment. The PowerFlex 525 drive is designed to meet industry standards for electromagnetic compatibility (EMC)‚ minimizing interference and ensuring compatibility with other equipment.
The drive offers various control modes‚ including speed control‚ torque control‚ and position control‚ providing users with flexibility in motor control applications. The PowerFlex 525 drive also incorporates advanced features like PID control‚ allowing users to precisely regulate motor performance. Its user-friendly interface simplifies configuration and operation‚ enhancing ease of use for operators. These technical specifications make the PowerFlex 525 drive a versatile and capable solution for various industrial applications requiring precise motor control.
Installation and Wiring
Installing and wiring the PowerFlex 525 drive requires careful attention to safety precautions and adherence to the manufacturer’s instructions. The drive’s compact design allows for flexible mounting options‚ enabling installation in various industrial environments. The manual provides detailed instructions for mounting the drive securely to a suitable surface‚ ensuring its stability during operation.
The wiring process involves connecting the drive to the motor‚ power supply‚ and control system. The manual provides clear wiring diagrams for various configurations‚ including direct-on-line (DOL) and variable frequency drive (VFD) setups. It outlines the specific wiring procedures for each configuration‚ including the selection and sizing of appropriate conductors and protective devices. The manual also highlights the importance of proper grounding and shielding to minimize electrical noise and ensure safe operation.
The PowerFlex 525 drive features a user-friendly terminal block that simplifies the wiring process. It provides clearly labeled terminals for each connection‚ minimizing the risk of errors during wiring. The manual provides detailed instructions for connecting the control signals‚ such as start/stop buttons‚ emergency stops‚ and other control inputs‚ ensuring proper communication between the drive and the control system. The user manual emphasizes the importance of testing the wiring thoroughly before powering up the drive to ensure correct connections and prevent potential hazards.
Configuration and Programming
The PowerFlex 525 drive offers a range of configuration options‚ allowing you to tailor its operation to specific application requirements. You can configure parameters such as motor type‚ voltage‚ current‚ and speed control modes to optimize performance and achieve desired results. The drive features a user-friendly keypad and display‚ enabling you to navigate through menus and adjust settings directly on the device.
The manual provides detailed instructions for configuring various aspects of the drive‚ including motor parameters‚ control modes‚ communication settings‚ and safety functions. It explains how to set up the drive for different applications‚ such as pump control‚ fan control‚ conveyor systems‚ and other industrial processes. The manual also guides you through the process of configuring the drive for communication with external devices‚ such as PLCs‚ HMIs‚ and other automation systems.
The PowerFlex 525 drive supports various communication protocols‚ including EtherNet/IP‚ DeviceNet‚ and RS-485. The manual provides detailed information on configuring the drive for each protocol‚ including the steps for setting up the network connection‚ assigning IP addresses‚ and configuring communication parameters. It also explains how to use the drive’s built-in communication features for data exchange‚ remote monitoring‚ and control.
Communication Protocols
The PowerFlex 525 drive supports a variety of communication protocols‚ enabling seamless integration with your automation system and providing flexibility in data exchange‚ remote monitoring‚ and control. These protocols allow you to connect the drive to PLCs‚ HMIs‚ and other devices‚ enabling you to monitor drive status‚ adjust parameters‚ and control motor operation remotely.
The manual provides detailed information on configuring the drive for each protocol‚ including the steps for setting up the network connection‚ assigning IP addresses‚ and configuring communication parameters; It also explains how to use the drive’s built-in communication features for data exchange‚ remote monitoring‚ and control; You can configure the drive to communicate using different protocols‚ such as EtherNet/IP‚ DeviceNet‚ and RS-485‚ allowing you to choose the protocol that best suits your application and existing infrastructure.
The manual includes comprehensive information on the supported protocols‚ such as the supported data types‚ communication speeds‚ and network topologies. It also provides troubleshooting tips for resolving communication issues and ensuring reliable data transfer between the drive and your automation system. By understanding these protocols and their configuration options‚ you can effectively integrate the PowerFlex 525 drive into your system and leverage its communication capabilities for enhanced functionality and control.
Troubleshooting and Maintenance
The PowerFlex 525 drive manual provides comprehensive guidance on troubleshooting and maintenance‚ ensuring optimal performance and minimizing downtime. It covers a wide range of topics‚ from identifying common issues to performing routine maintenance tasks. This section empowers you to diagnose and resolve problems efficiently‚ keeping your drive running smoothly and reliably.
The manual includes a detailed troubleshooting section that outlines common problems‚ their potential causes‚ and recommended solutions. It provides clear instructions on how to interpret fault codes displayed on the drive’s keypad or through communication protocols. You can easily identify the source of the issue and take appropriate action to rectify it. The manual also provides valuable information on preventative maintenance‚ including recommended inspection intervals‚ lubrication procedures‚ and cleaning guidelines. This ensures the longevity and optimal performance of your drive.
The manual includes sections on maintaining the drive’s internal components‚ such as the motor‚ encoder‚ and brake. It provides step-by-step instructions for cleaning‚ inspecting‚ and adjusting these components‚ ensuring their proper functionality. The manual also covers maintenance of external components‚ including the control panel‚ wiring‚ and connectors‚ ensuring a safe and reliable operating environment. By following the manual’s instructions for troubleshooting and maintenance‚ you can prolong the life of your PowerFlex 525 drive‚ ensuring its optimal performance and minimizing the risk of unexpected downtime.
Safety Precautions
The PowerFlex 525 drive manual emphasizes the importance of safety precautions‚ highlighting potential hazards and providing detailed instructions for safe operation. It outlines crucial safety guidelines and procedures to protect users and the equipment from potential risks. The manual emphasizes the need to adhere to all local and national safety standards and regulations‚ ensuring a safe working environment.
The manual includes sections on personal protective equipment (PPE)‚ highlighting the importance of using appropriate safety gear‚ such as gloves‚ eye protection‚ and safety shoes‚ when working with the drive. It also provides instructions on how to properly handle hazardous materials‚ such as oil and grease‚ ensuring safe handling and disposal. The manual emphasizes the need to follow proper lockout/tagout procedures before working on the drive‚ ensuring that power is completely disconnected and the system is safe for maintenance.
The manual includes specific guidelines for working with the drive’s electrical components‚ highlighting the dangers of high voltage and emphasizing the need to follow proper grounding and isolation techniques. It also covers safety precautions for operating the drive at high speeds‚ highlighting the importance of proper guarding and enclosure to protect users from potential hazards. The manual emphasizes the need to follow all safety instructions outlined in the manual and to seek professional assistance for any complex or unfamiliar procedures.
Applications and Use Cases
The Allen-Bradley PowerFlex 525 drive boasts a wide range of applications and use cases across various industries‚ demonstrating its versatility and adaptability. This drive‚ with its power rating of 0.4…22 kW (0.5…30 Hp)‚ finds its place in various applications‚ from simple motor control to complex automation systems. The drive’s ability to handle global voltage classes of 100…600V further enhances its versatility‚ making it suitable for diverse environments.
The PowerFlex 525 excels in applications requiring precise speed and torque control‚ such as conveyor systems‚ pumps‚ and fans. Its embedded EtherNet/IP adapter facilitates seamless integration into industrial automation systems‚ allowing for easy communication and control. The drive’s ability to handle both single and three-phase motors makes it ideal for various applications‚ including material handling‚ packaging‚ and processing industries.
The PowerFlex 525 drive is also well-suited for applications requiring advanced features‚ such as regenerative braking and closed-loop control. Its configurable I/O allows for customization to meet specific application requirements‚ while its robust construction ensures reliable operation in demanding environments. The drive’s ability to handle various motor types‚ including permanent magnet motors‚ expands its application range‚ catering to diverse needs and requirements across different industries.
The Allen-Bradley PowerFlex 525 drive stands as a testament to Rockwell Automation’s commitment to providing reliable and efficient motor control solutions. Its comprehensive features‚ including a wide power range‚ global voltage compatibility‚ and flexible mounting options‚ make it a versatile and adaptable drive suitable for a wide range of applications across various industries. The drive’s embedded EtherNet/IP adapter facilitates seamless integration into automation systems‚ enabling easy communication and control. The PowerFlex 525 drive is designed for ease of use‚ with its user-friendly interface and comprehensive documentation making it accessible for both novice and experienced users; The drive’s robust construction ensures reliable operation in demanding environments‚ minimizing downtime and maximizing productivity.
By combining advanced features‚ flexible configuration options‚ and a user-friendly interface‚ the PowerFlex 525 drive provides a compelling solution for various motor control applications. Whether you are seeking a drive for simple motor control or a complex automation system‚ the PowerFlex 525 drive offers the performance‚ reliability‚ and versatility needed to meet your specific requirements. Its seamless integration with Rockwell Automation’s comprehensive portfolio of automation solutions ensures a smooth transition into your existing systems‚ minimizing integration challenges and maximizing operational efficiency.