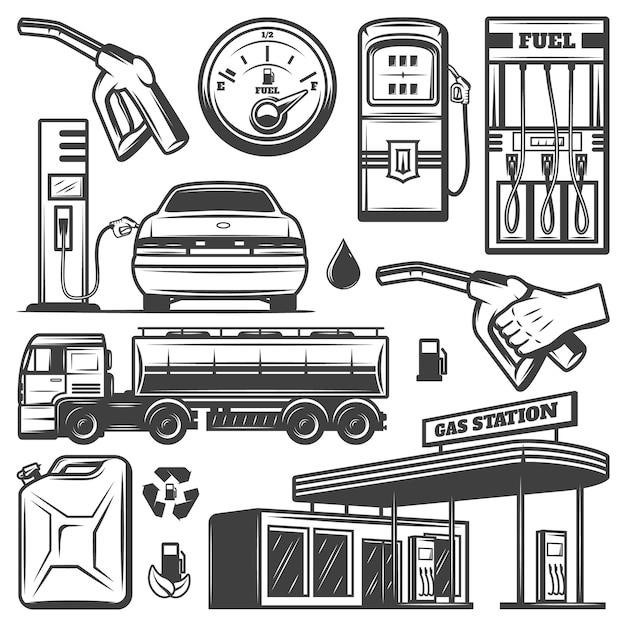
manual fuel pump
Manual Fuel Pump⁚ A Comprehensive Guide
This guide delves into the world of manual fuel pumps, exploring their types, applications, working principles, advantages, disadvantages, selection criteria, maintenance, safety precautions, and conclusion. It aims to provide a comprehensive understanding of these essential components used in various applications, from fuel transfer to automotive systems.
Introduction
In the realm of fluid handling, fuel pumps play a crucial role in transporting fuel from the storage tank to the engine, ensuring a continuous supply for combustion. While modern vehicles predominantly rely on electric fuel pumps, manual fuel pumps remain relevant in various applications, particularly in situations where electrical power is unavailable or impractical. These mechanical devices harness human power to move fuel, offering a reliable and cost-effective solution for a wide range of tasks.
Manual fuel pumps, often referred to as hand pumps, are essential tools in industries such as agriculture, construction, and marine, where they facilitate fuel transfer for equipment and machinery. They are also commonly employed in automotive applications, particularly in older vehicles or as backup systems when electric pumps fail. The simplicity and ruggedness of manual fuel pumps make them ideal for situations demanding portability and resilience in the absence of electrical power.
This guide will delve into the intricacies of manual fuel pumps, providing a comprehensive understanding of their different types, working principles, advantages, disadvantages, selection considerations, maintenance practices, and safety precautions. By exploring these aspects, we aim to equip readers with the knowledge necessary to utilize these essential devices effectively and safely.
Types of Manual Fuel Pumps
Manual fuel pumps come in a variety of designs, each tailored to specific applications and fluid handling requirements. The most common types include⁚
- Rotary Pumps⁚ These pumps feature a rotating impeller that draws fluid into the pump chamber and pushes it out through the discharge port. Rotary pumps are known for their high flow rates and efficiency, making them suitable for transferring large volumes of fuel. They are often employed in industrial and agricultural settings.
- Semi-Rotary Pumps⁚ Similar to rotary pumps, semi-rotary pumps use a rotating mechanism to move fluid. However, they typically have a simpler design and lower flow rates compared to their full-rotary counterparts. Semi-rotary pumps are often preferred for lighter-duty applications where portability and cost-effectiveness are paramount.
- Lever Pumps⁚ Lever pumps operate by using a lever to create suction and discharge pressure. The lever action creates a vacuum that draws fluid into the pump chamber, and then pushes it out through the discharge port. Lever pumps are often used for smaller volumes of fuel and are particularly useful for transferring fuel from drums or containers.
- Siphon Pumps⁚ Siphon pumps utilize the principle of gravity and pressure difference to transfer fluid. They consist of a flexible hose with a suction tube and a discharge tube. By creating a vacuum in the suction tube, the pump draws fluid from the source container and allows it to flow through the discharge tube to the destination. Siphon pumps are relatively simple to use and are well-suited for transferring fuel over short distances.
The choice of manual fuel pump depends on factors such as the type of fuel, flow rate requirements, portability needs, and budget constraints.
Applications of Manual Fuel Pumps
Manual fuel pumps find diverse applications across various industries and sectors, serving as reliable tools for fluid transfer and handling. Some of their key applications include⁚
- Fuel Transfer⁚ Manual fuel pumps are extensively used for transferring fuel from drums, tanks, or vehicles to other containers or equipment. This is particularly common in agricultural settings, construction sites, and industrial facilities where fuel storage and distribution are crucial.
- Automotive Applications⁚ In older or classic vehicles, manual fuel pumps are sometimes employed to deliver fuel from the tank to the engine. These pumps typically operate using a lever or handle to create suction and pressure. Modern vehicles, however, predominantly rely on electric fuel pumps for greater efficiency and reliability.
- Marine Applications⁚ Manual fuel pumps are used in marine settings for transferring fuel from storage tanks to fuel lines or outboard engines. They are also employed for priming fuel systems and for emergency fuel transfer in case of electrical system failures.
- Industrial Applications⁚ Manual fuel pumps play a vital role in various industrial processes where fuel handling is essential. These applications include fuel transfer for generators, machinery, and other industrial equipment. They are also used for transferring other liquids, such as oil and kerosene.
- Emergency Response⁚ In emergency situations, manual fuel pumps can be crucial for transferring fuel to vehicles or equipment in areas where electrical power is unavailable. Their portability and simple operation make them valuable tools for disaster relief and emergency response efforts.
Manual fuel pumps offer a reliable and cost-effective solution for fluid transfer in various applications, providing a manual alternative to electrically powered pumps.
Working Principle of a Manual Fuel Pump
Manual fuel pumps operate on a simple yet effective principle based on suction and pressure to transfer fuel from a source to a destination. The mechanism typically involves a lever or handle that, when actuated, creates a vacuum within the pump chamber. This vacuum draws fuel from the source tank or reservoir through an inlet pipe. As the lever is released, the pump chamber is sealed, and pressure builds up within the chamber. This pressure forces the fuel through an outlet pipe, delivering it to the desired location.
There are various types of manual fuel pumps, each employing slightly different mechanisms to generate suction and pressure. However, the fundamental principle remains consistent⁚ creating a vacuum to draw fuel in and then building pressure to push it out. The efficiency of the pump depends on factors such as the design of the pump chamber, the size of the lever or handle, and the type of materials used.
The operation of a manual fuel pump is typically characterized by a repetitive pumping action, where the lever or handle is repeatedly actuated to maintain a continuous flow of fuel. The rate of fuel transfer depends on the pumping speed and the efficiency of the pump. The pump’s ability to create a vacuum and generate pressure is crucial for effective fuel transfer, ensuring a steady flow of fuel to the desired destination.
Advantages of Manual Fuel Pumps
Manual fuel pumps offer several advantages, making them a suitable choice for various applications, especially in situations where electricity or other power sources are unavailable or impractical. One of the primary benefits is their simplicity and reliability. Manual fuel pumps have fewer moving parts compared to their electric counterparts, reducing the likelihood of breakdowns or malfunctions. This makes them particularly well-suited for use in harsh environments or situations where maintenance access may be limited.
Another key advantage is their portability. Manual fuel pumps are typically compact and lightweight, making them easy to transport and use in various locations. Their portability is particularly valuable in applications involving fuel transfer in remote areas or where access to stationary pumps is restricted. Additionally, manual fuel pumps are often cost-effective compared to electric pumps. This makes them an attractive option for individuals or businesses with limited budgets or for applications that require infrequent use.
Furthermore, manual fuel pumps are environmentally friendly. They operate without relying on external power sources, reducing energy consumption and minimizing carbon emissions. This makes them a sustainable choice for fuel transfer in environmentally sensitive areas or for applications that prioritize eco-conscious practices.
Disadvantages of Manual Fuel Pumps
While manual fuel pumps offer several advantages, they also come with certain drawbacks that should be considered before choosing them for a particular application. One of the primary limitations is their relatively low flow rate. Manual pumps rely on human power to generate the pressure needed to transfer fuel, which can be a time-consuming process, especially for large volumes. This can be a significant disadvantage in applications where time is a critical factor, such as refueling vehicles or transferring fuel for industrial purposes.
Another disadvantage is the physical exertion required to operate manual fuel pumps. Pumping fuel manually can be physically demanding, particularly for extended periods or when transferring heavy fuels. This can be a concern for individuals with limited physical strength or for applications involving frequent or prolonged use. Additionally, manual fuel pumps may not be suitable for applications requiring high pressure or high flow rates. Their design limitations make them less effective in situations where substantial pressure is needed to overcome resistance or where large volumes of fuel need to be transferred quickly.
Furthermore, manual fuel pumps can be susceptible to wear and tear, especially if they are not properly maintained or used in harsh environments. This can lead to reduced efficiency or premature failure, requiring repairs or replacements. It is crucial to select a pump made from durable materials and to follow proper maintenance procedures to maximize its lifespan and ensure reliable performance.
Choosing the Right Manual Fuel Pump
Selecting the appropriate manual fuel pump for a specific application is crucial to ensure optimal performance, safety, and longevity. Several factors should be considered when making a decision, including the type of fuel to be transferred, the flow rate required, the pressure needed, the operating environment, and the budget. For instance, when transferring diesel fuel, a robust pump with a high flow rate and pressure capability is essential, while a lighter-duty pump might suffice for transferring gasoline.
The intended flow rate is another critical consideration. If large volumes of fuel need to be transferred quickly, a pump with a high flow rate is necessary. Conversely, for smaller volumes, a pump with a lower flow rate may be more suitable. The pressure requirement also plays a role in pump selection. Some applications require higher pressure to overcome resistance or to deliver fuel to a specific location. The operating environment should also be factored in. If the pump will be used in a harsh environment, such as extreme temperatures or exposure to corrosive substances, a pump made from durable materials with corrosion resistance is essential.
Finally, the budget is an important factor to consider. Manual fuel pumps vary in price depending on their features, materials, and brand. It is essential to balance the required features with the available budget to make an informed decision. By carefully considering these factors, you can choose the right manual fuel pump for your specific needs, ensuring a safe, efficient, and reliable fuel transfer process.
Maintenance and Care of Manual Fuel Pumps
Proper maintenance and care are essential to ensure the longevity and optimal performance of manual fuel pumps. Regular inspections, cleaning, and lubrication can prevent premature wear and tear, ensuring reliable operation. Before each use, visually inspect the pump for any signs of damage, such as cracks, leaks, or missing parts. Check the hoses for any kinks or damage, and ensure the connections are secure. It is important to note that different pump models may have specific maintenance instructions, so it is crucial to consult the manufacturer’s manual for detailed guidance.
Regular cleaning of the pump is crucial to prevent clogging and ensure smooth operation. This can be done by removing any debris or sediment accumulated in the pump housing and the hoses. For cleaning, use a mild detergent and water, avoiding harsh chemicals that could damage the pump. After cleaning, thoroughly rinse the pump and allow it to dry completely before reassembling. Lubricating the pump’s moving parts, such as the handle and the piston, with a suitable lubricant can reduce friction and wear, extending the pump’s lifespan.
Storing the pump properly after use is important to prevent damage and ensure a long service life. Store the pump in a clean, dry environment, protected from dust, moisture, and extreme temperatures. Avoid storing the pump with fuel inside, as it can degrade the pump’s internal components over time. By following these maintenance and care tips, you can ensure your manual fuel pump operates reliably and efficiently for many years to come.
Safety Precautions When Using Manual Fuel Pumps
Using manual fuel pumps requires a keen awareness of safety precautions to prevent accidents and ensure a safe working environment. Fuel is highly flammable, so it is crucial to work in a well-ventilated area to minimize the risk of fire or explosion. Avoid using the pump near open flames or heat sources. Always ground the pump and the fuel container to prevent static electricity buildup, which can ignite flammable vapors.
Before handling fuel, ensure your hands are clean and dry, and wear appropriate safety gear, such as gloves and eye protection. Avoid spills and leaks, and immediately clean up any spills with a non-flammable absorbent material. When transferring fuel, avoid overfilling the container, leaving adequate space for expansion. Always use the correct pump for the type of fuel you are transferring, as using the wrong pump can damage the pump and pose a safety hazard.
Ensure the pump is properly connected and secured to the fuel container and the receiving container. During operation, keep a firm grip on the pump handle to prevent accidental disconnection or spills. After use, carefully disconnect the pump and store it properly to prevent accidental activation. Always use caution when handling fuel and follow the manufacturer’s instructions for safe operation of the manual fuel pump. By adhering to these safety precautions, you can minimize the risk of accidents and ensure a safe working environment.